Directional Drilling Background
Hydrocarbons are a vital part of any modern economy representing a primary source of energy extensively used by industrial, power and transport sectors. Demand for hydrocarbons grows every day placing huge pressure on the upstream petroleum sector. The upstream petroleum sector is responsible for acquiring hydrocarbon resources while also processing them for energy demands. A petroleum reservoir is a subsurface pool of hydrocarbons, oil and or gas, trapped in rock formations. Reservoirs are porous rock sealed by overlaying rock that creates a trap for hydrocarbons migrating through the earth’s crust toward the surface. Traps containing economically viable accumulations of hydrocarbons are accessed by drilling down a mile or more to the hydrocarbon trap and then isolating the well with steel pipe and cement to allow the hydrocarbon to flow to the surface.
Introduction To Directional Drilling
Increase in the demand for hydrocarbons and the associated high levels of production from conventional hydrocarbon traps has led toward the depletion of conventional hydrocarbon reservoirs. Depletion of conventional reserves has increased focus on exploration of harder to produce hydrocarbons such as deep water and unconventional reservoirs. Due to the difficulty of producing unconventional reservoirs, productivity must be increased by drilling long, up to three miles, extensions laterally through the formation. To drill such complex wells requires drillers to control the direction of the well in three dimensions. Directional drillers must first drill straight down then drill a curve at the bottom of the well to land in the reservoir and then follow the reservoir so the well does not leave the oil-bearing rock and become unproductive.
Directional drilling is also used to achieve subsurface targets that are away from the surface well location or in the event it is necessary to bypass some geological feature present in the subsurface that can cause complexity during drilling, e.g., a fault. Directional drilling is also used for killing blown out or uncontrolled wells. During directional drilling the wellbore path is continuously monitored to keep it moving in the right direction. Parameters that are measured during directional drilling include inclination, azimuth, dog leg severity, etc. This information is measured by using measurement while drilling (MWD) tools/services and recorded in the deviation survey of the well bore.
What are Directional Drilling Services?
Now that you are familiar with directional drilling, we would like to review types of directional drilling services and the main providers of these services. Directional drilling is a complex procedure and it involves sophisticated equipment and specialized staff to hit the subsurface target efficiently. Directional drilling services are provided by oil and gas service companies with the main players in the field of directional drilling services being Halliburton, Schlumberger, Baker Hughes, Compass, Cougar, and Nabors etc. The primary services employed during directional drilling are directional drilling, geo steering, measurement while drilling and logging while drilling. These sophisticated processes include tools and specialized staff necessary for the success of any directional drilling job. Exploration and production companies typically turn to directional drilling service companies for service, tools and human resources.
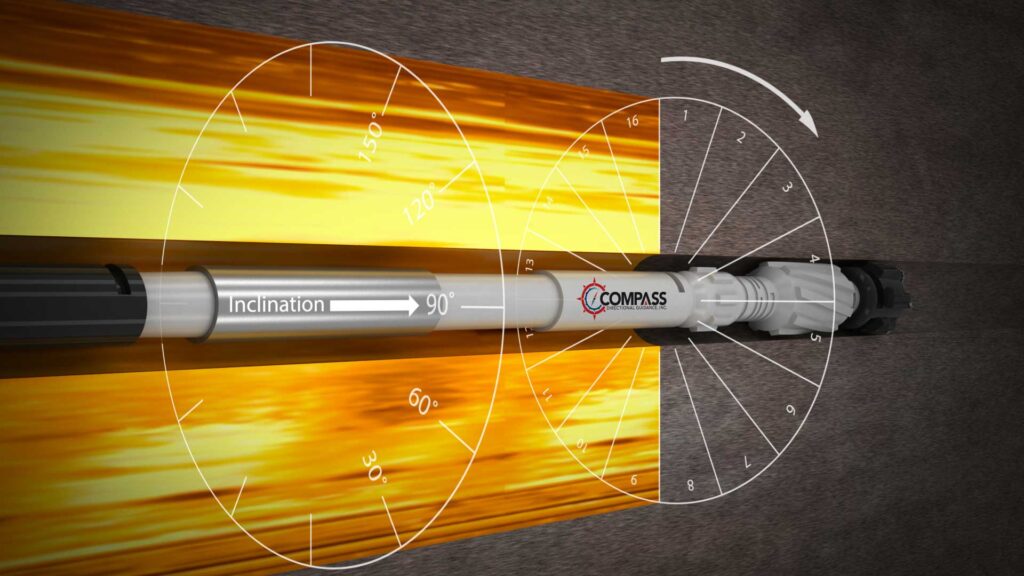
Tools Used During Directional Drilling
Directional drilling is the drilling process in which the drill string is guided every foot of the way to remain as close to the well design or plan as possible. Sophisticated tools are used to measure the precise location allowing the directional driller to set the trajectory of the well going forward. At times it is necessary to guide the vertical section of the well but it is critical to guide the curve and the horizontal section.
Directional drilling equipment includes drill bits, mud motors and rotary steerable systems. The mud motor is a progressive cavity positive displacement pump that is incorporated in the drilling string. The motor provides additional power to the bit energizing the drilling process efficiently. Much like a turbine, drilling mud produces torque or rotational energy in the power section of the mud motor. The configuration of the rotor and the stator is used in the mud motor to enhance the efficiency of the drilling process. To increase the efficiency of the mud motor in terms of horsepower the number of lobes and power assembly length are increased. So, without a mud motor in the drill string, the bit rotates only with speed of the rotary table on the rig, but with the mud motor there is extra rotation and torque applied to the bit.
Rotary Steerable System (RSS)
The rotary steerable system is used to steer the wellbore angle by using rotation from the surface. If the rig is equipped with a rotary steerable system then there is no need for the mud motor. One more advantage of the rotary steerable system over a mud motor is that it preserves the borehole quality. With rotary steerable systems the direction of the wellbore is inclined by using the surface system. Most RSS systems have closed loop control so adjustments are made continuously down hole without the need of a command from a directional driller. The deviation of the wellbore is achieved during continuous rotation and eliminates the need to start and stop the rotary table to orient the bit to steer. The two main mechanisms used by rotary steerable systems to deviate the well bore are ‘push the bit’ and ‘point the bit’. The primary disadvantage of rotary steerable systems is their high cost compared to mud motors.
Measurement While Drilling (MWD)
Measurement while drilling is another important service that is associated with directional drilling. MWD, measurement while drilling, is done to report the position and orientation of the bit and to log the record of the wellbore path navigating to the subsurface target with accuracy and efficiency. MWD tools measure directional data accurately in the well bore and are connected with a surface control station via telemetric connections. MWD engineers monitor the real time data and inform directional drillers about well direction. The data, post processing and interpretation, is recorded as wellbore deviation survey data. The main parameters that are recorded during the MWD process are the direction of the wellbore in terms of azimuth, the inclination of the wellbore from the vertical, the dogleg severity, etc. The wellbore path is tracked in three dimensions by using the afore-mentioned parameters to avoid any inaccuracy in the well path. The MWD services are also provided by service companies like Schlumberger, Halliburton, Weatherford, Compass, Cougar, etc.
Why Logging While Drilling Was Introduced?
Directional drilling results in the inclination of the well path at various angles. In some cases, the well path is nearly horizontal. Horizontal wells are sometimes drilled in reservoirs to increase exposure to reservoir hydrocarbons. In horizontal wells the conventional logging, i.e., wireline logging is very challenging to run because it can cause cable conveyed tool strucking. So, to overcome this problem, logging while drilling was introduced. Logging while drilling also eliminated the need for conventional logging reducing the time to drill a well.
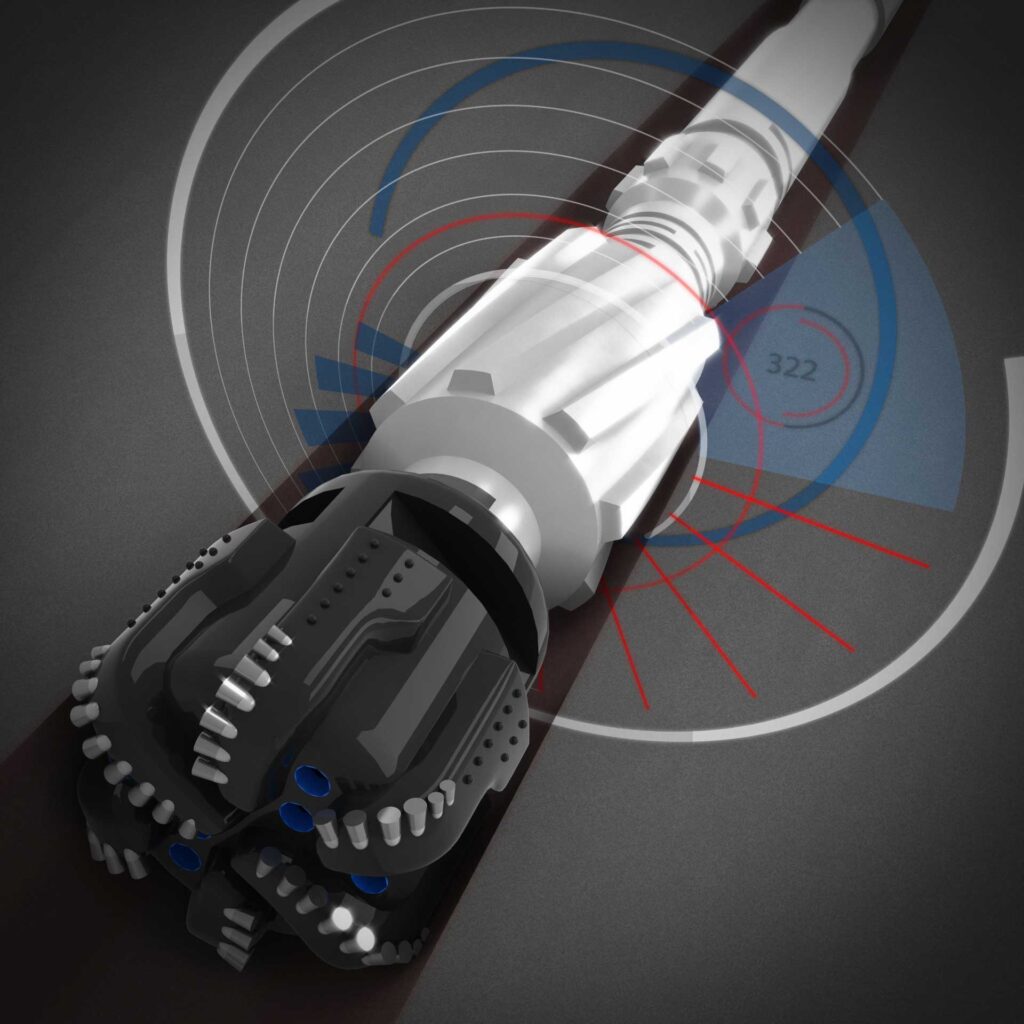
Logging While Drilling (LWD)
In logging while drilling the logging tools are run in to the wellbore as a part of the drill string. The physical properties of rocks (logging measurements) are acquired simultaneously with the drilling process. LWD includes gamma ray logging, density logging, resistivity logging, neutron logging, caliper logging and sonic logging. Logging while drilling tools are part of the bottom hole assembly (BHA) of the drill string and communicate to the surface logging control station via mud telemetry, electromagnetic waves or through drill pipes via a wire. LWD tools are also equipped with solid state memory devices that can be retrieved after LWD tools come to surface. The logging data is then processed by the LWD Engineers present at the wellsite and sent to the client company for interpretation. The specialized tools used during logging while drilling have the ability to work under intense borehole conditions (high temperature and pressure) with the primary limitation of logging while drilling being its high cost and high tool replacement time. If the LWD tool fails downhole, it requires the complete tripping of drill string to replace the tool which requires a lot of time. LWD services are generally used in concert with directional drilling. The main LWD service providers are Schlumberger, Weatherford, Halliburton and Compass.
Conclusion
The increased demand of hydrocarbons has focused the attention of exploration and production companies towards unconventional hydrocarbon resources. The unconventional hydrocarbon reservoirs, especially shale gas reservoirs, are drilled by using specialized tools and technologies. Service companies providing directional drilling service allow for the drilling of deviated wellbores to achieve harder earned subsurface targets. This has largely been a US story but China and more recently Abu Dhabi are targeting unconventional resources in their countries. More are sure to develop their own unconventional resources as time goes on.
Tool and equipment services for directional drilling, measurement while drilling and logging while drilling are all services that work in concert to ensure the achievement of desired targets by keeping track of the wellbore path providing suitable understanding of the subsurface information. The modern upstream industry and world energy economics now require more unconventional resources than ever before and directional drilling is regarded as an important technology for the exploration and production sector.